Table of Contents
Concrete Pavers (Introduction)
Concrete pavers are a precast concrete product made of Plain Cement Concrete (PCC). They are used for outdoor flooring such as house lawns, patios, parking areas and public walkways. Concrete pavers are available in the market in different sizes and shapes as per user requirements. Concrete pavers are very popular due to their durability and ease of installation and removal.
Concrete pavers designs

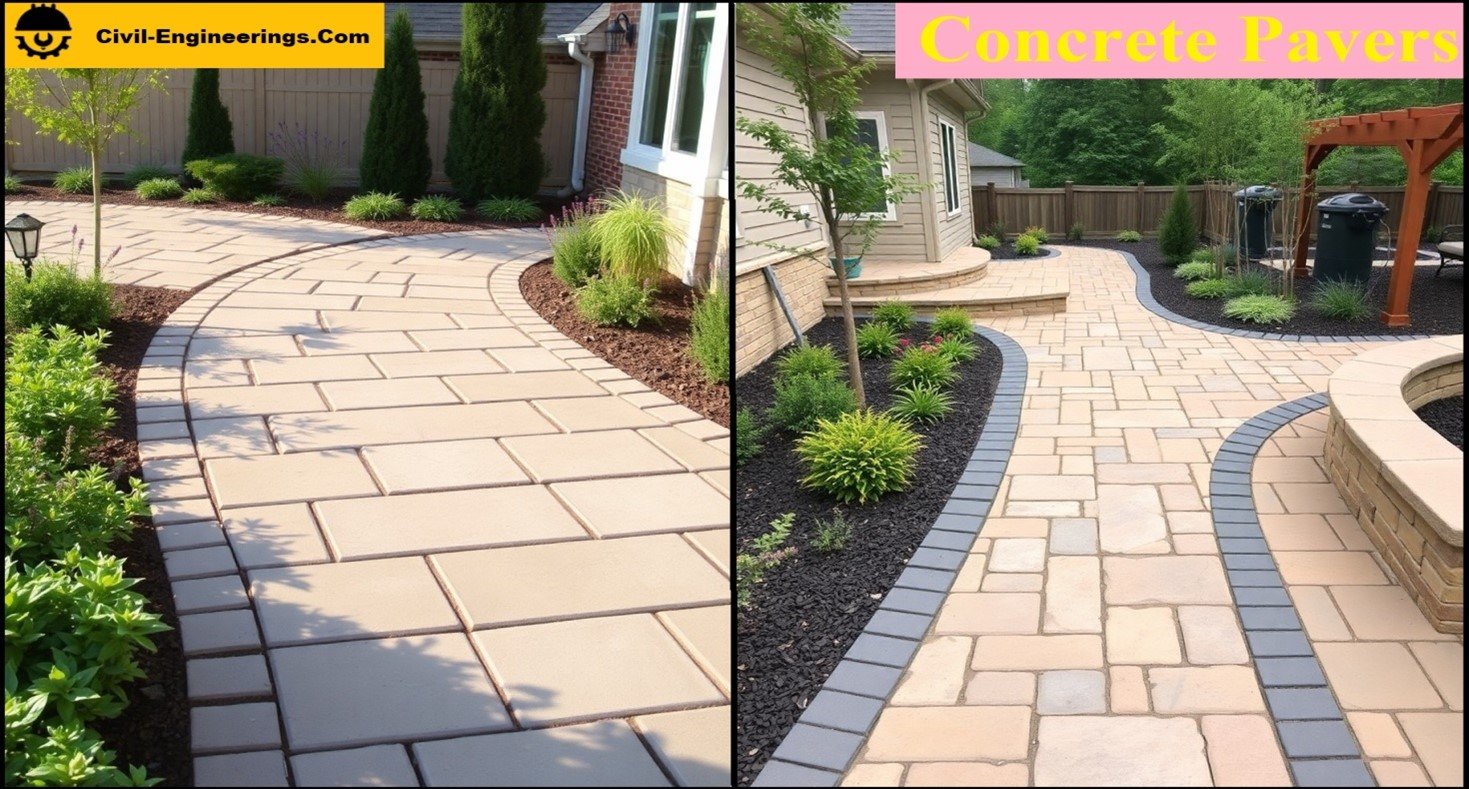


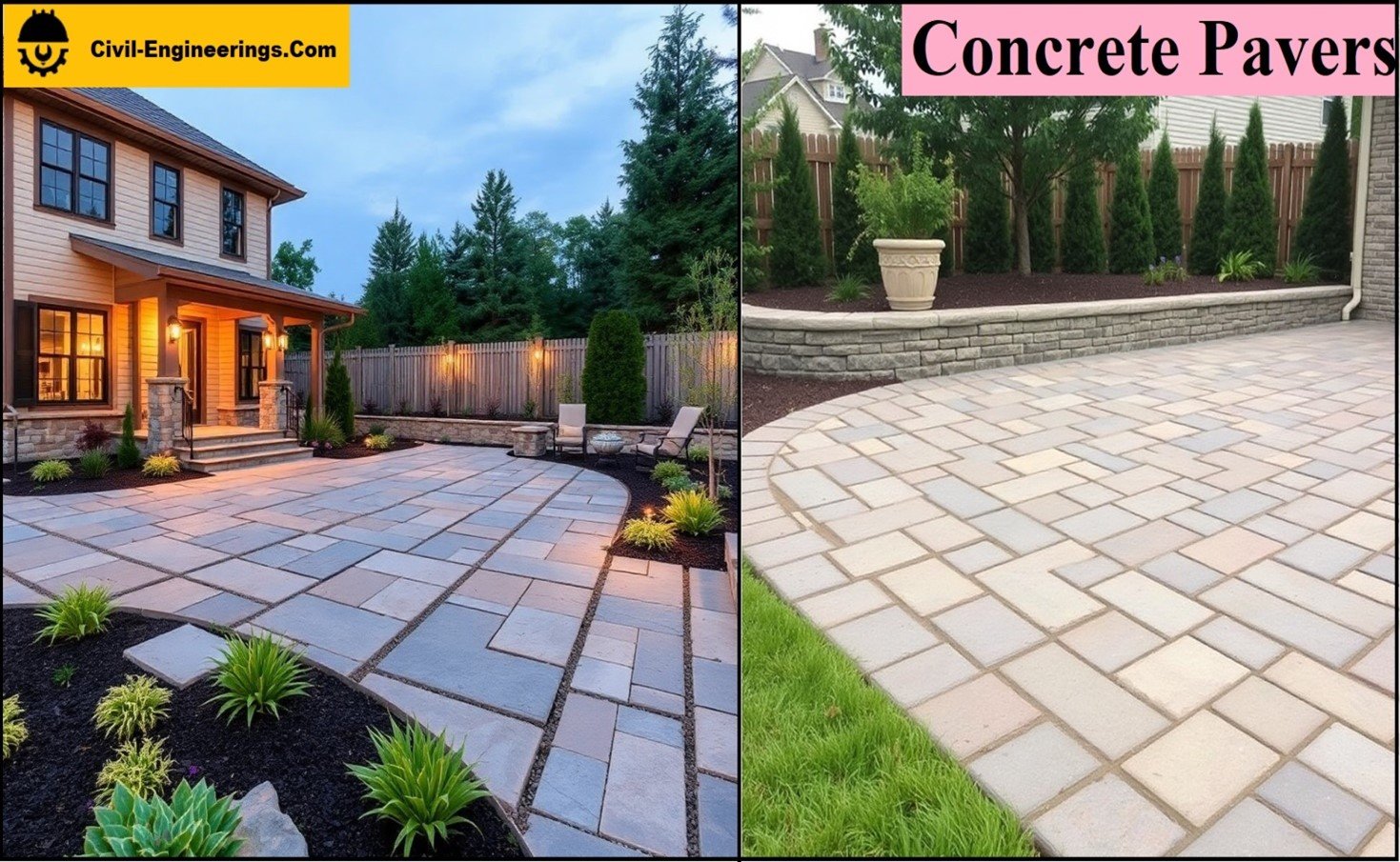
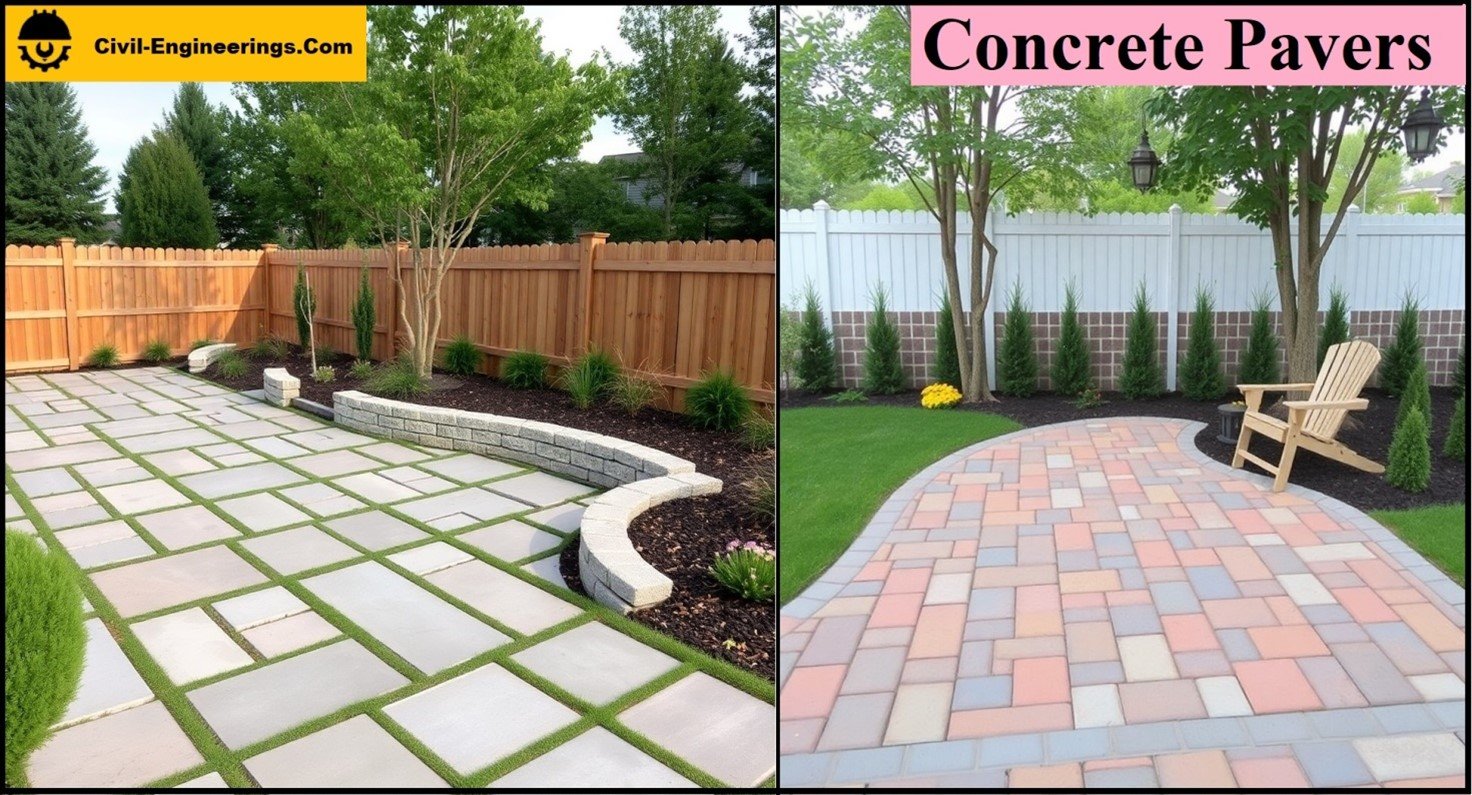
Concrete Pavers Installation Process
It is very important that concrete pavers should install as per professional practices to achieve the desired results. The installation process involves several steps as outlined below:
Site Preparation
Site preparation is the first step of concrete paver installation. This step includes excavation, filling and compaction of the natural ground. If the site is below the required level, filling will be done and if the site is above the required level, excavation or cutting will be performed. After filling or excavation, compaction is the most important step. It should be carried out properly, either manually or using mechanical compaction tools like compactor or roller.
Base Installation
After site preparation, the next step is laying the base material, typically made of crushed stone or gravel to provide a stable and permeable foundation. The base layer should be thoroughly compacted and leveled by using a plate compactor to prevent settling over time. The thickness of the base depends on the load bearing capacity of the pavers. For light duty pavers, it should not be less than 3 inches (76 mm), for medium duty and heavy duty, the thickness should not be less than 4 inches (100 mm) and 8 inches (204 mm) respectively.
Bedding Sand Layer
Spread a 1inch layer of coarse sand over the base material and level the sand by using a screed to create a smooth surface for placing the pavers.
Paver Placement
After bedding sand layer now process of place the concrete pavers will start. Concrete paver should place in desired pattern, starting from one corner or edge and working systematically. Uniform spacing should maintain between pavers using spacers or by eye.
Edge Protection
After completion of paver installation edge protection is very important to keep the pavers in place and prevent shifting over time. Edge protection can be plastic, metal or concrete.
Joint Sand Filling
Spread polymeric or regular sand over the pavers and sweep it into the joints. Compact the pavers again to ensure the sand settles firmly between the joints.
Final Compaction and Cleaning
At last perform a final compaction to lock the pavers in place. Sweep away excess sand and clean the surface.
Types and Usage of Concrete Pavers
Type of concrete paver is based on required bearing capacity of pavers. Concrete pavers are categorized into three types light duty, medium duty and heavy duty. Light duty concrete pavers are used at Residential, drive way, walk ways, parking patios etc. Medium Duty concrete pavers are used Residential, Streets, Public Parking, service road, maintenance area, canal lining, storage area, City petrol pumps etc. Heavy Duty concrete pavers are used City Streets, Loading deck Industrial floors, Highway petrol pumps etc.
Standard thickness and Strength of Concrete Pavers
Standard thickness of Light duty concrete paver should not less than 50 mm, for Medium Duty and Heavy Duty should not less than 60 and 80mm respectively. Min 28 days Cylinder Compressive strength for Light duty concrete paver shall be 35 MPa (5000 psi) and for Medium Duty and Heavy Duty shall be 48 MPa (7000 psi).