Table of Contents
Granular Sub Base (Introduction)
Granular Sub Base is critical components of road construction, providing support and stability to the base course & pavement layers. This layer helps distribute the load of traffic and prevent premature failure of the road surface.
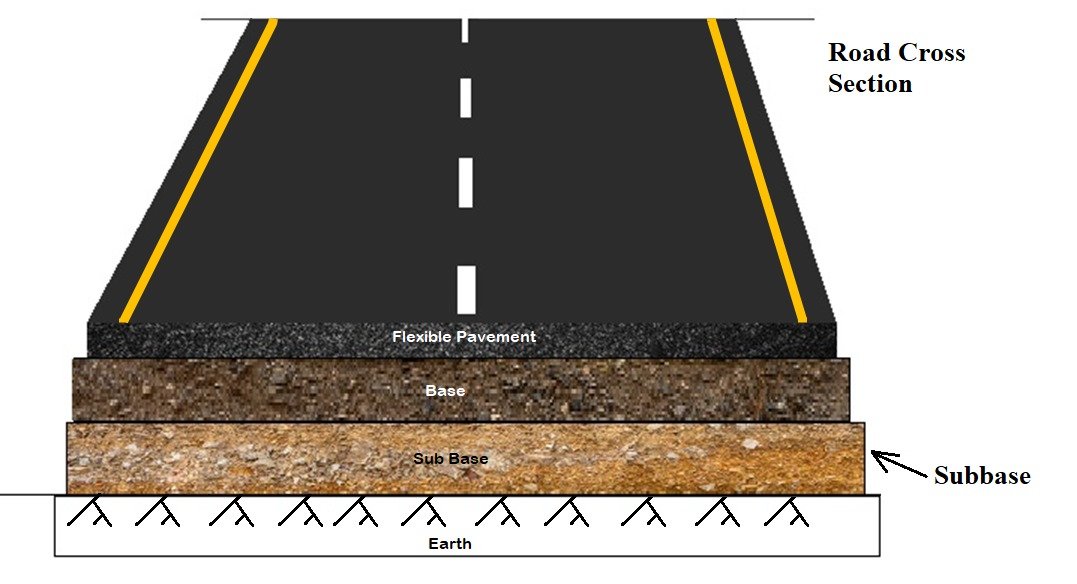
The Granular Sub Base (GSB) is the layer of material placed on the compacted subgrade and beneath the base course. It provides additional support and helps in drainage. Common materials used for Granular Sub Base include crushed stone, gravel or recycled concrete. The Granular Sub Base layer is typically thicker than the base layer.
Construction Process of Granular Sub Base
a. Preparation of Subgrade Surface
Before dumping and placing subbase material surface of subgrade should be prepared and any unsuitable material should removed.
b. Placement of Granular Sub Base material
Spread the sub-base material evenly over the prepared sub-grade using equipment like bulldozers, graders or excavators. The layer thickness should conform to design specifications. Granular Sub Base includes all naturally occurring materials, meeting the requirements mentioned in below Table:


Other Properties of Granular Sub Base
- CBR Value (tested as per AASHTO T-193): 30% (Min)
- Plasticity Index (P.I): 6 (Max)
- Liquid Limit (L.L): 25 (Max)
- Abrasion Value: 50% (Max)
- Sand Equivalent (S.Eq): 25 (Min)
Soil aggregates subbase available in nature consisting of pebbles, shingle and sand may be used. It may be a mixture of natural and crushed stone. The pebble size should not exceed 60 mm (2½”).
c. Compaction of Granular Sub Base Material
Initial Rolling
Begin compaction immediately after spreading the material. Use heavy rollers (either pneumatic-tired rollers or vibratory rollers) to achieve initial compaction. This process helps in settling the material and removing air voids.
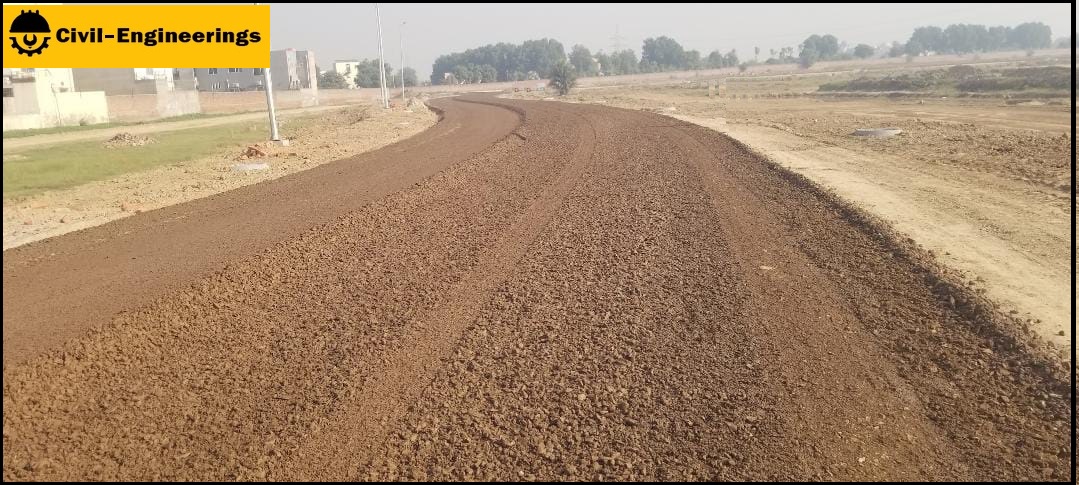
Moisture Control
Control the moisture content of the Granular Sub Base material. It should be moist enough to facilitate compaction but not too wet, which can cause instability. Moisture content is typically controlled to a specified range based on material type and conditions.
Layer-by-Layer Compaction
Depending on the thickness of the sub-base layer, it may be compacted in several layers. Each layer is typically compacted to a specified density using the compaction equipment.
Overlap
Ensure that each pass of the compactor overlaps the previous pass by at least half the width of the roller to achieve uniform compaction.
Number of Passes
The number of passes required for compaction depends on factors such as material type, thickness and moisture content. Generally, minimum 6 passes are required to achieve the desired density.
d. Testing
Compaction tests are performed on each 15cm layer to ensure that the Granular Sub Base layers meet the required specifications. Min Compaction (Field Density) 98% of MDD determined as per ASTM -D 1557
Important Points regarding Granular Sub Base
- Use hard, suitable and approved materials
- Lay to full depth, hand pack on edge and fill interstices with spalls of sub-base material.
- Lay to gradients, camber and super-elevation required and dry roll to a solid even finish with 8 - 12 Ton power roller. The actual weight of the roller may be changed at the discretion of the Site Engineer, according to the nature of soil and the (bottoming) sub base materials used.
- Make good with spalls of bottoming materials any voids, which may appear during the process of compaction and rolling, so as to leave the finished surface solid and conforming to the required slopes, levels etc.
- The thickness refers to the thickness after compaction.
- If bricks are allowed to be used, they shall be over burnt, whole bricks close laid flat or on edge. Spread sand to fill voids and interstices @ 0.15 Cum per 10 Sqm.